Your operators will often play a significant role when it comes to pinpointing issues that have an impact on OEE (Overall Equipment Effectiveness). Nobody has as much first-hand experience with equipment as Operators who spend time using the equipment day in and day out. Operators will be the first to spot any quality issues, inefficiencies, and breakdowns as soon as they arise. Ensuring that your Operators are included in problem solving and continuous improvement processes can lead to even better results and more efficient operations.
There is a world of opportunity when it comes to creating efficiency on your manufacturing shop floor. In our latest blog, we’ll be exploring OEE. Starting with the basics and then delving into some key points to consider when implementing OEE on your shop floor. We’ll also be looking at the vital human element that makes OEE so effective.
The development of OEE
Let’s start with the development of OEE. Over the years, manufacturing processes grew to be more and more complicated, meaning that manufacturers could no longer rely on old school Breakdown Management processes that simply meant that when a machine broke down, it was repaired. Following the era of Breakdown Management was Productivity Management, which enabled Production Teams to be directly involved with Maintenance and Repair processes. However, there was still the looming issue of Equipment Availability that continued to obstruct manufacturers from reaching their full potential. This is where OEE comes into the picture.
What is OEE?
Now considered a significant Key Performance Indicator (KPI) for many manufacturers, OEE is virtually ubiquitous across a variety of industries and is used to measure, monitor, and evaluate the efficiency and effectiveness of a production process. OEE provides a numerical value (usually in the form of a percentage %) that represents the overall productivity of an entire production line or machine. OEE takes 3 main factors into consideration; Availability, Performance, and Quality, which outline the 6 big losses.
6 Big Losses:
- Machine malfunctions and unplanned equipment downtime
- Changeover time and malfunctions
- Idle time and short stops
- Reduced production speed
- Scrapped units
- Rework
OEE
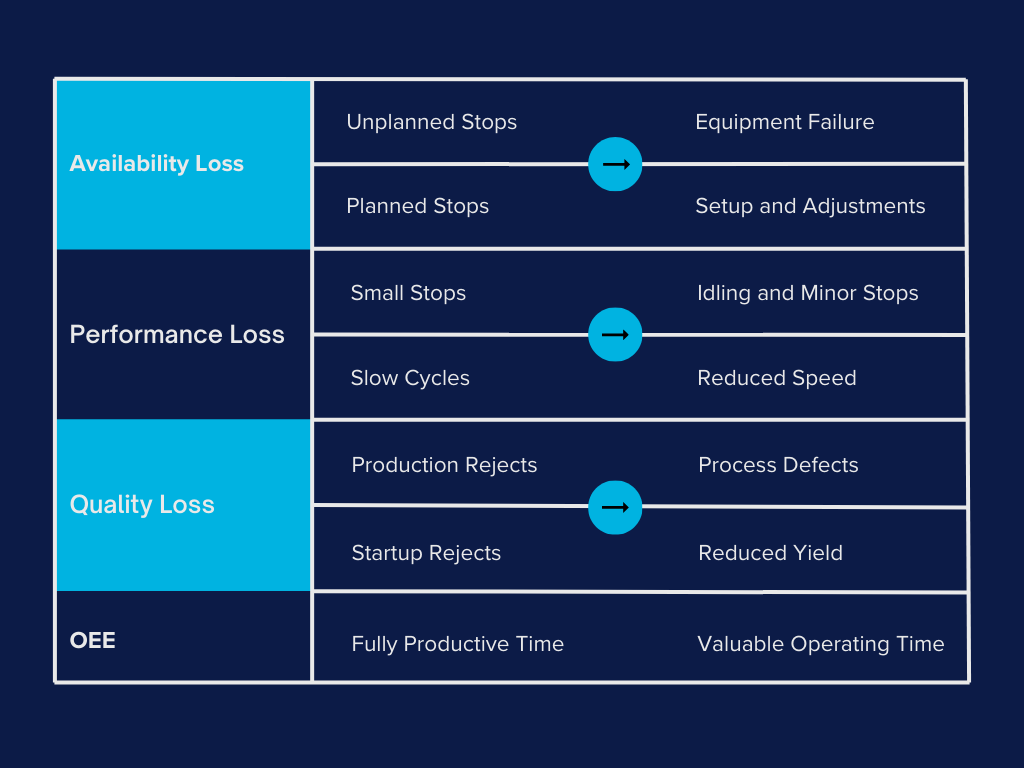
How to calculate OEE
#1 Availability
- The Availability factor measures the actual operating time of the equipment versus the scheduled or planned time. It accounts for downtime due to maintenance, breakdowns, changeovers, and any other reasons the equipment isn’t running when it’s supposed to (excluding lunch breaks).
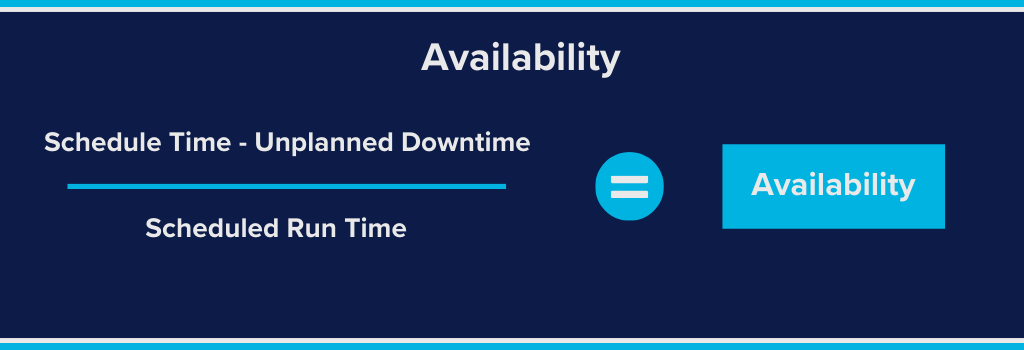
#2 Performance
- Performance refers to the speed or rate at which the equipment runs compared to its designed or ideal speed. It considers factors like minor stops, reduced speed, and other issues that impact the machine’s performance.
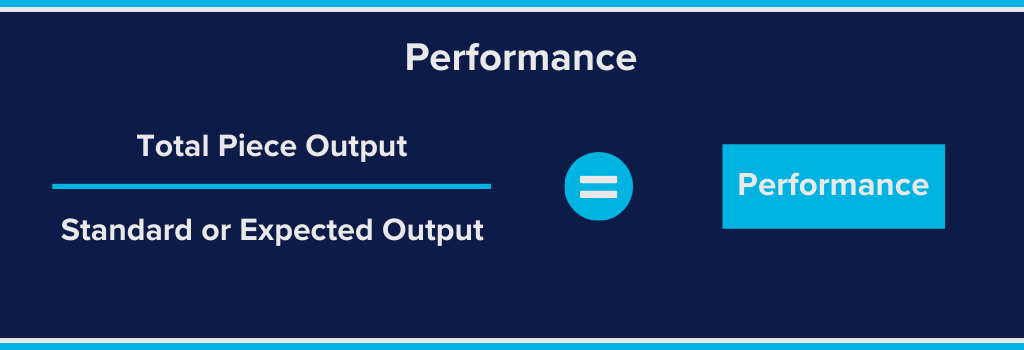
#3 Quality
- Quality measures the good output of the equipment compared to the total output. It considers defective products, errors, or items that don’t meet the required quality standards.
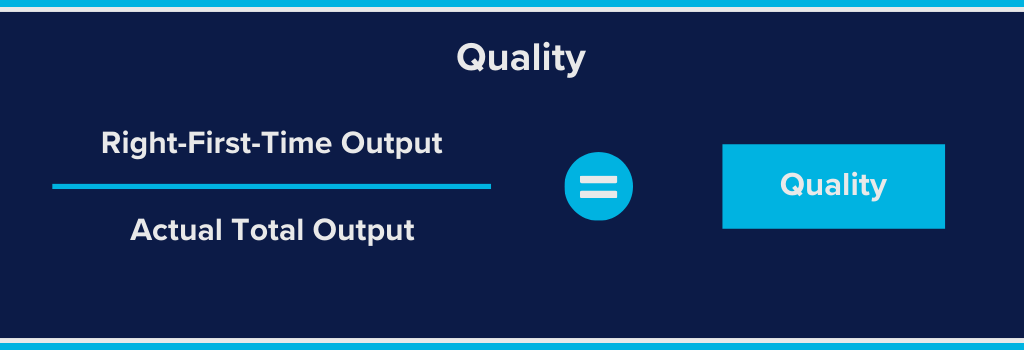
The OEE Formula
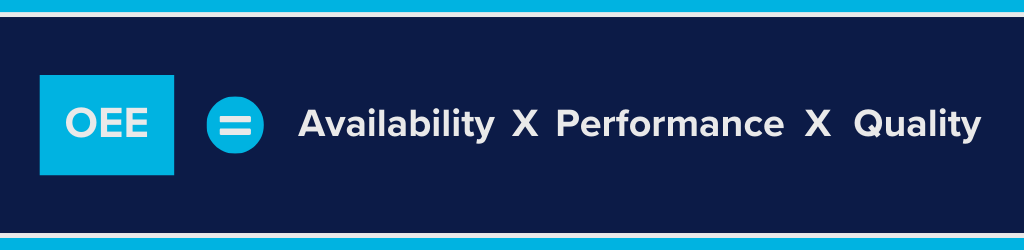
- The benefits of OEE in manufacturing:
OEE can have a pretty substantial impact on your manufacturing processes. By making the effort to analyze OEE, manufacturers can experience the following benefits:
Identify and eradicate inefficiencies
The deficiencies that cause equipment downtime, performance issues, and quality defects are easily identified using OEE. Whether you are experiencing equipment failures, tool failures, excessive Operator errors, or poor maintenance. OEE provides information that allows manufacturers to create targeted improvements that reduce waste and increase overall productivity.
Optimize manufacturing processes:
The ability to understand where, why and how inefficiencies take place gives manufacturers the confidence to make better informed decisions that optimize equipment usage, reduce downtime, and enhance overall output based on the data that is available to them.
Continuous improvement:
OEE is often used as part of a broader continuous improvement strategy such as Kaizen or Six Sigma. By regularly monitoring and analyzing OEE data, manufacturers can identify areas for improvement and implement changes to continually enhance operational efficiency.
Employee Engagement:
Getting your employees to engage in the improvement process can be a tremendous challenge. However, implementing an OEE process can help to get employees more engaged. By involving employees when identifying and implementing improvements and making OEE data more transparent, manufacturers can foster a culture of continuous improvement and accountability.
Overall Equipment Effectiveness is a crucial metric for assessing the performance of manufacturing equipment. It helps manufacturers identify areas for improvement, reduce waste, enhance productivity, and make more informed decisions to optimize their production processes.

- OEE: Driven by the human process.
So, the benefits of OEE are pretty clear, however it is equally as important to appreciate how effective the human element of OEE is. Consider the changes that OEE has on daily operations and workflows. Operators will need to adjust the way that they schedule, choose production targets, or maintenance routines to optimize equipment performance. OEE is just as much about the people as it is the equipment and processes. Overall equipment effectiveness is the backbone of many manufacturing facilities and ultimately allows them to achieve the goals they set out for themselves.
How can OEE positively impact my workforce?
- Workplace Safety: There is also the opportunity to create a safer working environment when equipment operates more efficiently. Think about how much you could reduce the risk of accidents that could potentially harm workers by having equipment that continuously operates at peak performance, reducing the risk of unexpected breakdowns.
- Training & Skill Development: Implementing an OEE strategy will often require you to cross-train your employees, particularly when it comes to troubleshooting issues, or managing equipment. This can motivate workers to take on more varied and challenging roles as they get the opportunity to further develop their skillset and can potentially improve job satisfaction.
- Employee Morale: It can be difficult to motivate workers, particularly if their role is highly process driven and repetitive. However, when workers see their efforts contributing to improved OEE, they can feel a sense of accomplishment and fulfilment. Seeing their work result in better overall productivity and improved product quality can have a positive impact on morale.
- Incentives and Rewards: Many companies will link performance related incentives to OEE and overall production efficiency. For employees, this means that OEE improvements could lead to bonuses or rewards for workers who make the effort to achieve, improve and maintain overall equipment effectiveness.
All in all, OEE can be a highly effective tool for manufacturers and it can take your current process from ineffective to high-yielding if implemented in the correct way. If you would like a solution that can transform your manufacturing processes, get in touch with the team at NoMuda by emailing info@nomuda.com or head over to the contact us page.
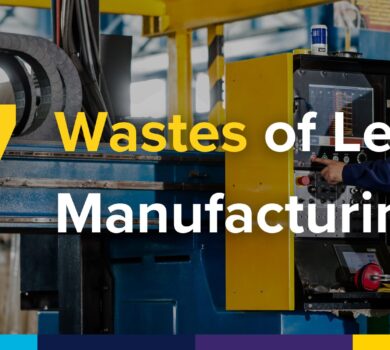
7 Wastes Of Lean Manufacturing
Introduction Muda is the Japanese word for waste, the inevitable and unwanted gremlin of every
Elevating Oil and Gas Equipment Manufacturing with NoMuda VisualFactory
Oil & Gas. In the competitive landscape of the oil and gas industry, the stakes
Have You Heard the News? NoMuda VisualFactory has been recognized as a 2023 Customers’ Choice
We at NoMuda are super-thrilled to be recognized as a Customers' Choice for September 2023