Introduction
Muda is the Japanese word for waste, the inevitable and unwanted gremlin of every shop floor. When Toyota first began developing the Toyota Production System (TPS) in 1948, they identified 7 Mudas (types of waste), and actively tackling these Mudas resulted in a much leaner production line.
Before you can get rid of something, you need to have found it. This blog will reveal what those 7 Wastes of Lean Manufacturing are, how you identify them and, most importantly, how to remove them. So, let us move on to the first Muda which is, appropriately…
1. Transportation
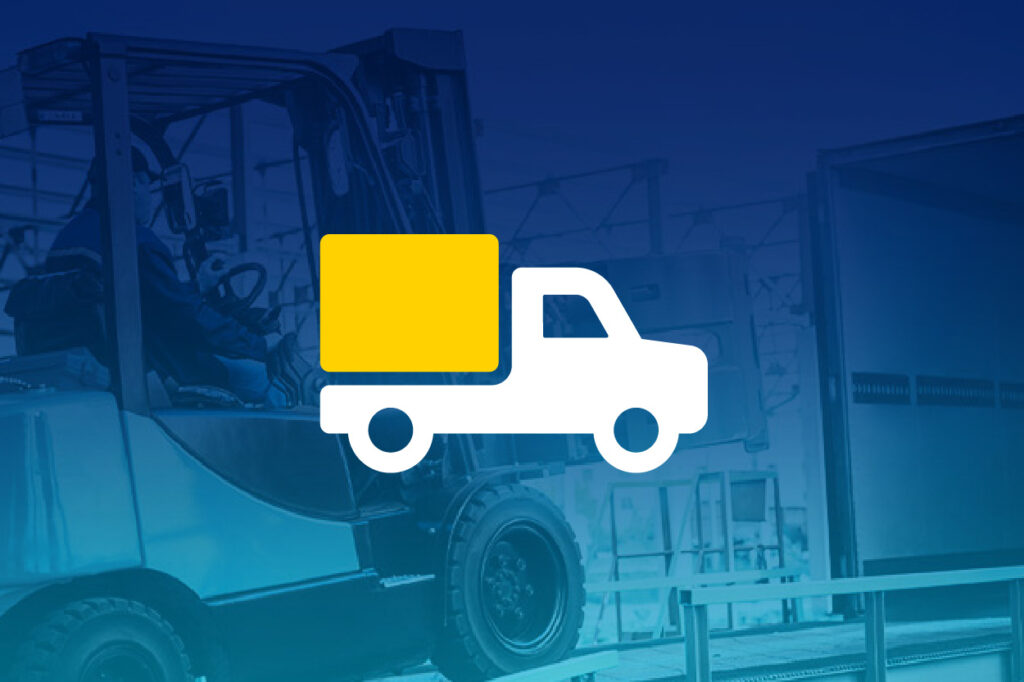
The transportation of products does not directly add to the product’s value. However, excessive transport will lead to the undesired costs that occur when the steps in your operation do not flow smoothly. And not just within your production facility; streamlining your supply chain to ensure goods are in the right place at the right time also helps eliminate waste due to transportation issues.
Reducing transportation waste in your production facility can be easier than you think. Mapping out your production facility and adapting its layout so that connecting operations are integrating smoothly with each other is a further way to eliminate transportation waste.
Reshaping your shop floor to allow for quick movement between workstations might seem like a huge investment, but the transportation of your products, be they completed or Work in Progress (WiP) items, often make a huge impact on your production lines efficiency, but it is not the only type of movement that does. Which takes us to the next Muda…
2. Motion
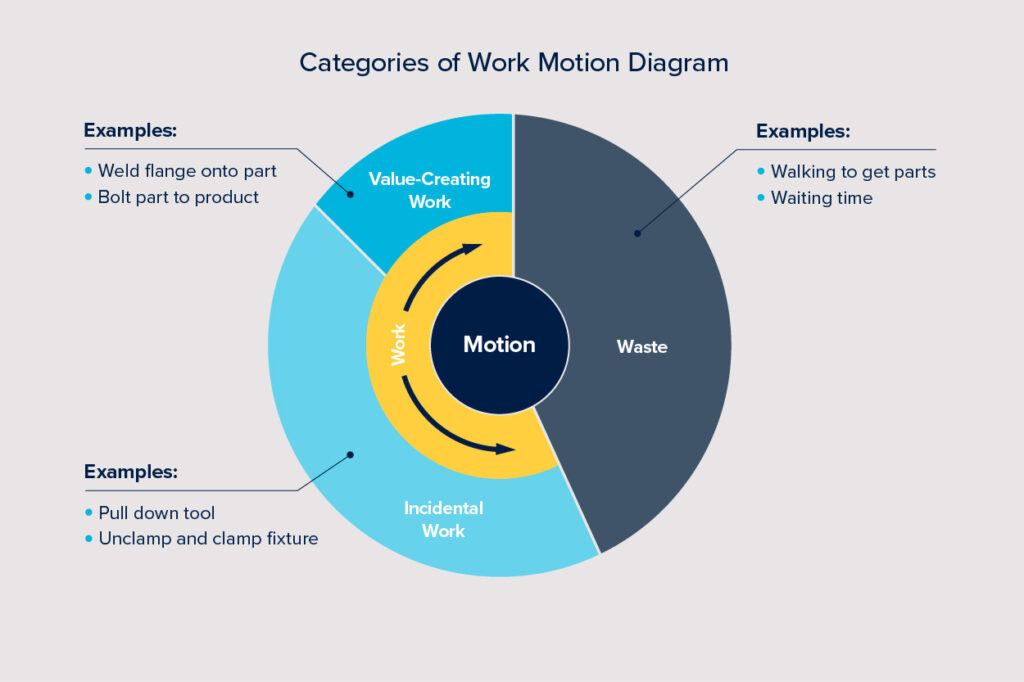
Motion refers to the movement of the workers within your production line. This ranges from the time and effort required for operators to move between workstations to the bending and stretching involved in obtaining and using the tools and equipment within a workstation.
They may seem minor, but if your operator is continually having to unnecessarily move around to obtain and utilise the tools and items they need, it all adds up, often massively degrading the speed your product progresses through your production line.
Reducing motion waste is just like removing transportation waste, but on a smaller scale. And it is not just the equipment, the workstation itself needs to be easily accessible for the operators working there. And, as a bonus to speeding up production, reducing all that unnecessary stretching and movement usually reduces the risk of possible harm for your operators and products.
But, while unnecessary motion is an issue, so are unnecessary pauses, which takes us to our next Muda.
3. Waiting
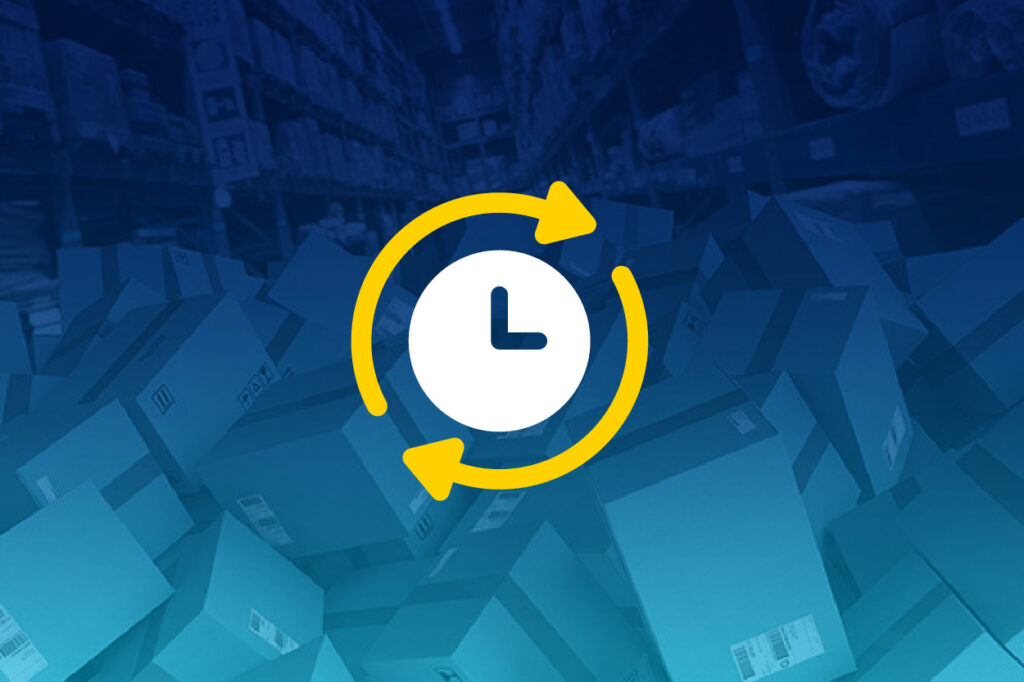
Waiting, as a waste, refers to products or WiP items either not being processed or not progressing through your production line. This can occur when your shop floor’s material flow is poor, or your production cycle times are too long. Many manufacturers use a ‘Batch Production’ process and move products along in the 5 or 10 seconds between each workstation. This can appear efficient when you see the 10 products in a batch delivered simultaneously, but this is often at the cost of operators waiting to complete a previous batch.
Eliminating waste caused by Waiting can be done by linking processes together, ensuring WiPs reach their desired destination at the exact time they are needed. You can also implement a ‘one piece flow’ system where, as soon as an operator is finished, the item is passed to the next workstation as soon as it is possible to do so.
https://www.youtube.com/watch?v=qeC35K1hxog
But let us not get carried away with making stuff …
4. Overproduction
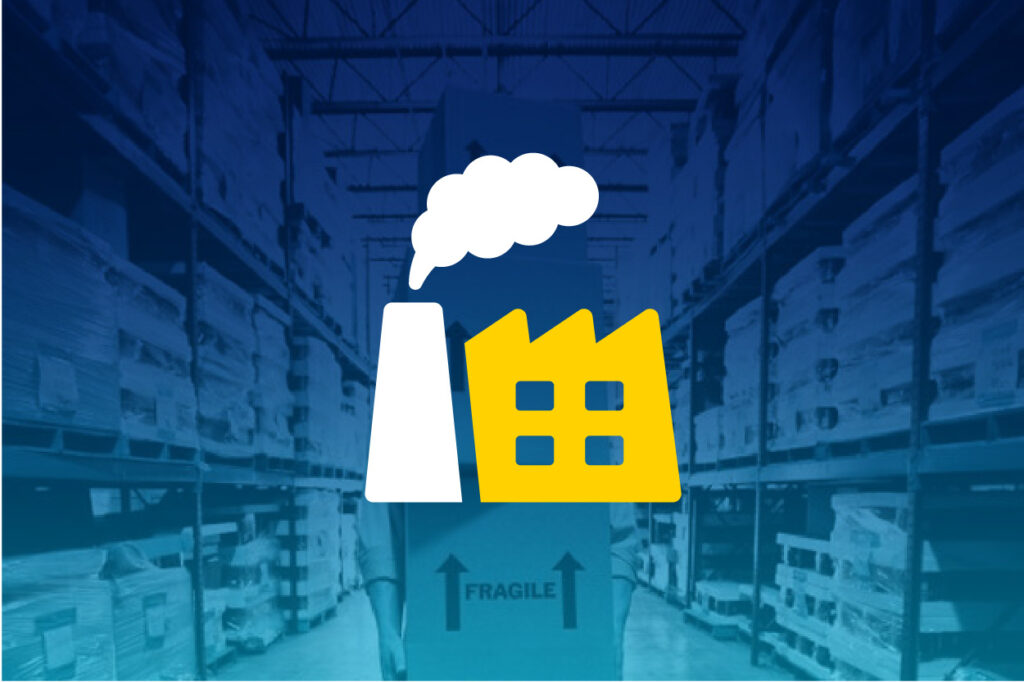
A common occurrence in the manufacturing space, overproduction as a waste can occur when you are manufacturing an item before it is required. Whether because it has yet to be ordered or yet to have a use within the production line, overproduction can be extremely costly and disrupt the flow of materials on your shop floor.
When implementing Lean Manufacturing processes, there is a danger that the rapidity of production will lead to overproduction. It is important to remember that Lean Manufacturing is about operating your production line with care as well as speed.
Solving an overproduction problem involves implementing a Just-In-Time production strategy where WiP items are specifically created as and when they are required. Keeping those communication channels open between your operators and your supervisors is so vital to eliminating overproduction wastes.
Working smarter is often a better substitute for working harder, which takes us nicely into the next Muda …
5. Overprocessing
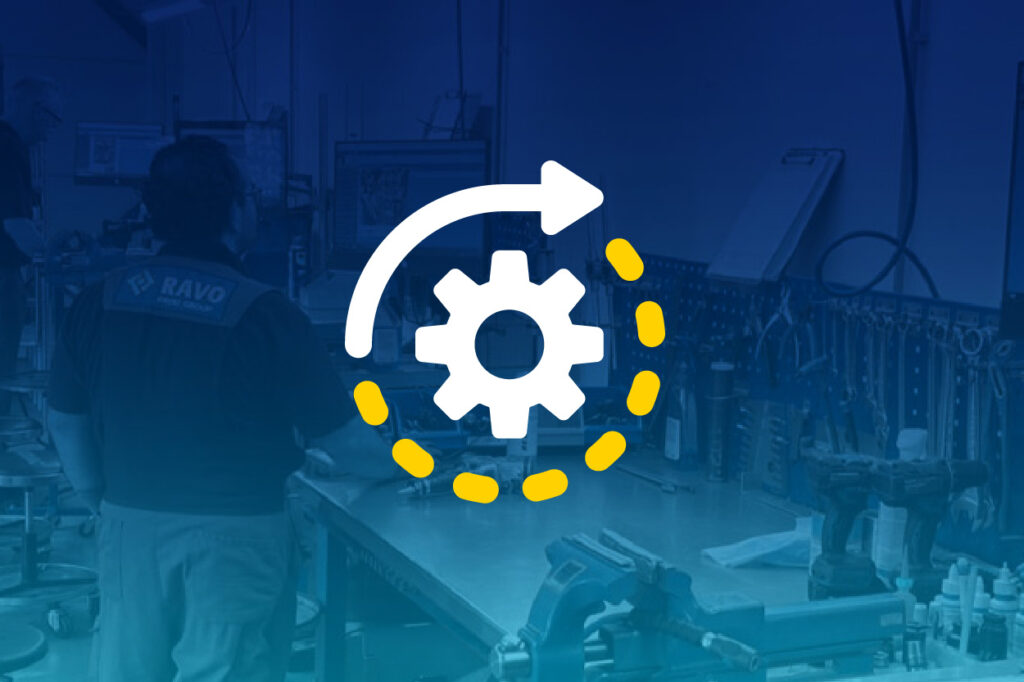
Testing and checking each product’s integrity is vital to creating a successful production line, but the over-processing of products and WiP items can have a huge impact on your production lines flow.
These redundancies often occur when operators are not being given clear and direct support, whether that be through poor work Instructions or a disorganised workstation (or production line). This leads to errors which must be dealt with by regularly checking items as they progress through production.
If you watch the following short videos, you can compare between how things used to be done by the German car manufacturer Trabant’s ‘Quality Assurance’ system to that of Audi (recognised in the past for their Lean Manufacturing).
Trabant Quality Control:
Audi Quality Control:
Can you see how Audi’s right-first-time processes obtain ‘Quality Assurance’ not by hammering pieces into the right place and slamming parts shut, but by ensuring the product’s quality as quickly, efficiently and consistently as possible?
And overprocessing doesn’t just mean the over-checking of potential faults along your production line. It also includes identifying the best time and place for each job within your production line and then removing those areas where work is being duplicated for no reason. To sum up, strip those redundancies back and merge those unnecessarily repeated processes into one efficient process.
And while you’re taking stock of that, you should also consider the next Muda…
6. Inventory
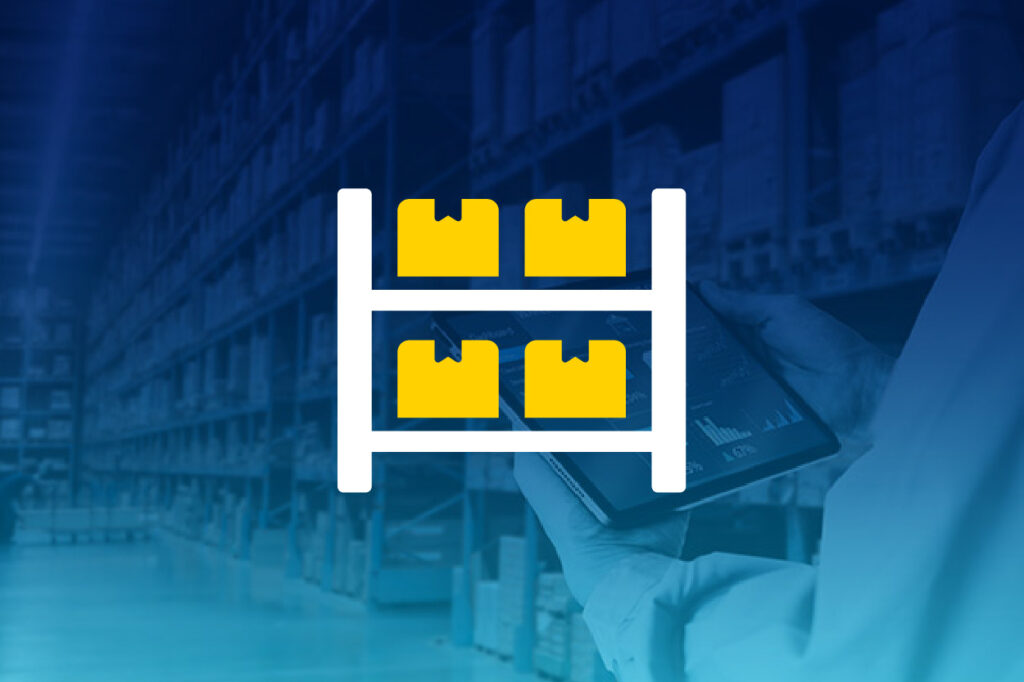
The overstocking of an inventory does more than take up space on your shop floor. Overused space can be a significant drain on financial resources whilst increasing lead times and delaying the checking of products.
Inventory Waste doesn’t just include finished products waiting for delivery, it is also the items you use to create products. By implementing a Just-In-Time strategy, you can be sure to reduce over-usage of inventory space and the related costs it often incurs. Having said that, you may want to take the hit of some inefficiency to allow for a contingency plan that caters for issues which can occur in the supply chain of your components or raw materials.
However, your shop floor is finite and the space should be allocated wisely. As with the previous Mudas, anything that forces over-movement reduces lead times and increases costs. So, to tackle this Muda, we need to allocate space for items relevant to each workstation, to give the operators fast access to what they need, and we also need to allocate a suitable space for items to be delivered, where they are out of the way of the rest of your production line.
The quality of your product will be dependent on the quality of your components and/or raw materials used, which takes us to our last Muda…
7. Defects
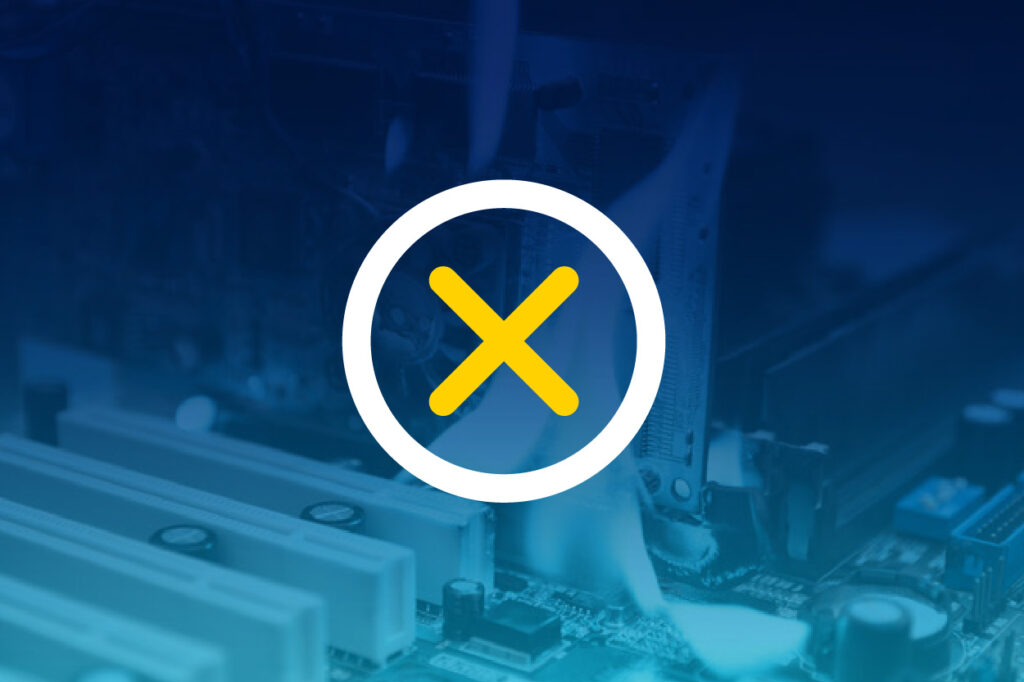
Product Defects can be very costly. Increasing the number of inspections can catch faults but the wastage cost will already have been inflicted and increasing inspections will create overprocessing waste.
Reducing defects before they occur is a preferable alternative. Bear in mind there’s no easy fix to eliminating all the possible errors and the most complicated parts of your production line will involve operators who are only human.
Quality assurance is such a key part of a supply chain, but the best way you can make sure your operators are making fewer mistakes, and so increase the chances of your products passing the quality assurance stage of your production line, is by supporting your operators with clear and unmistakable Work Instructions. Whether you digitize your Work Instructions or fully implement them within workspaces, making sure your operators can quickly and easily understand their Work Instructions is so very vital to removing Defect Waste.
The seven Mudas I’ve just outlined can (and often do) overlap, so don’t be surprised if, when you resolve one Muda issue, another waste of a different Muda type is simultaneously resolved. Every part of your shop floor is interrelated in some way and smoothing the processes between workstations, supporting the operators, and streamlining your production output should reward you with rapid improvements across your whole production line.
We at NoMuda have helped manufacturers across the globe streamline their production line processes with MES VisualFactory. A tool that digitizes your operators’ Work Instructions and documentation on your shop floor, reducing waste and making everything, from data collection to updating Work Instructions, so much easier and efficient.
If you would like to know more, do get in touch with us at info@nomuda.com